Electric Vehicles and Aerospace Applications
Overview
Electric vehicles (EVs), including hybrid, plugin-hybrid, and all-electric vehicles represent the future of both land and air transportation. EVs are nearly three times more efficient than traditional gasoline vehicles, and produce fractions of the greenhouse gas. EVs also have favorable characteristics for drivers, including full torque at zero speed, no required multi-gear transmission, and significantly reduced noise compared to gasoline vehicles.
The earliest EVs were invented in the 1830s, and obtained broad market share in the late 19th century, representing 38% of all vehicles on the road in 1900. Due to advances in internal combustion engines, EVs completely disappeared from the market by 1935. In the 1990s, GM's EV-1, and later the Toyota Prius - the first commercial hybrid electric vehicle (HEV) - catalyzed renewed interest in electric propulsion technologies. As of 2014, more than 665,000 EVs had been purchased worldwide.
Above the road, air- and space-craft are becoming increasingly electrified. Electronic actuators are gradually replacing the traditional pneumatic systems on commercial aircraft. Over the next two decades NASA Roadmaps hope to transition commercial aircraft to hybrid electric propulsion to reduce the nearly 8.5 billion gallons of fuel[1] used by US commercial flights in 2015.
Even higher, satellites and space exploration rovers are powered by electric photovoltaic panels. Continued space exploration is reliant on advances in extreme environment electronics.
Role of Power Electronics
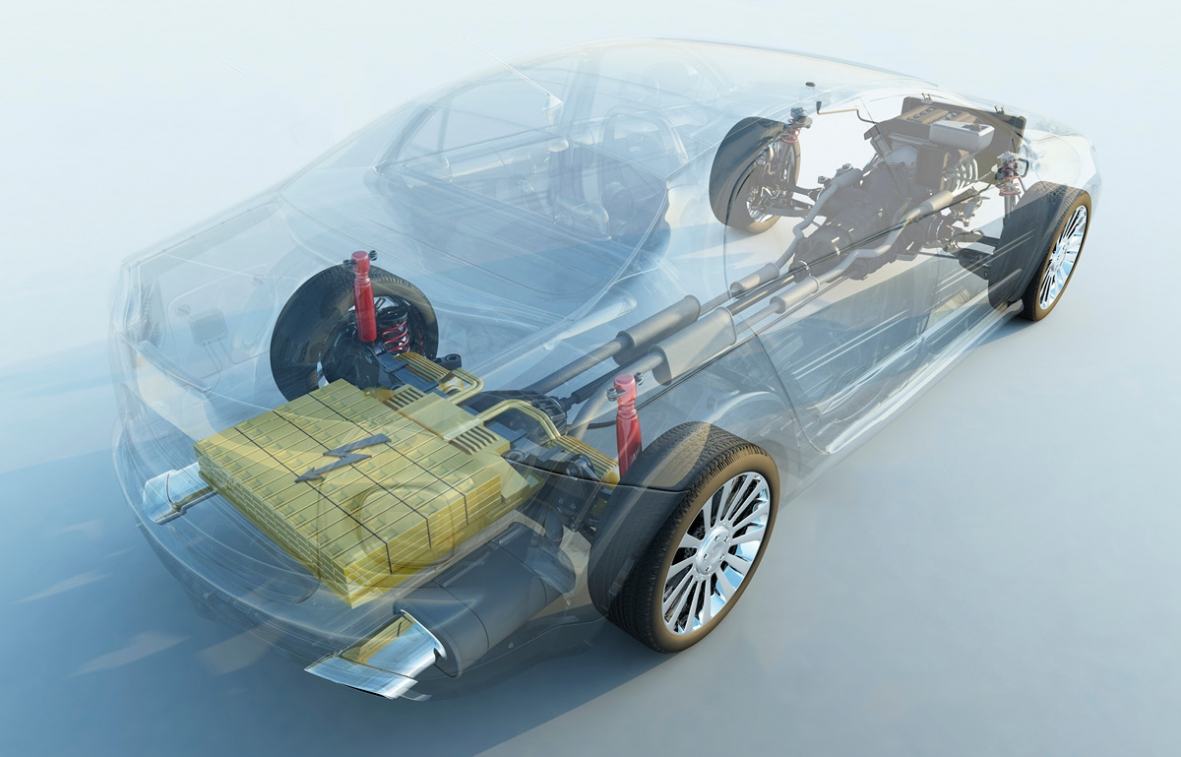
HEV powertrain system[2]
Power electronics constitute the heart of the electric vehicle powertrain, converting and controlling energy flow between the battery and electric motor. In many vehicles, a DC/DC converter is connected to the battery to boost from the 200-400 Vdc battery voltage to a higher, 600 Vdc bus. Doing so decouples the design of the battery from the motor and increases the efficiency of the motor at high power. Following this DC/DC, or directly from the battery if it is omitted, is an inverter. The inverter converts from DC to AC voltages, and regulates the currents driving the motor to the control speed and torque produced. In most vehicles, the inverter is a three-phase voltage-source inverter (VSI) rated for anywhere from 20 kW in hybrid vehicles to 150 kW in high performance EVs. Both the DC/DC and inverter are capable of both forward (traction) operation and reverse (regenerative) power flow. Today, most of these converters use silicon IGBTs, as the most cost-effective solution for high current, high power converters.
In plugin hybrid and pure electric vehicles, a separate converter is used to control battery charging when the vehicle is parked. These chargers may be on-board or off-board, and vary in power level from 1 kW to 100 kW, with the latter resulting in full charging times of less than one hour, and the former suitable for overnight recharging. Chargers convert AC voltage from the power grid to DC voltage or current to charge the battery. Typically, a two-stage structure is used, with an AC/DC rectifier managing power factor correction (PFC) which ensures that the converter does not distort the AC grid voltage, and a cascaded DC/DC stage which controls how power is delivered to the battery to ensure fast charging without degrading the battery.
Beyond the powertrain, relatively low-power conversion is present throughout the vehicle. Each of the on-board electronic controllers and actuators requires its own supply, with power derived from the high voltage battery and/or low-voltage (commonly 12V lead acid) battery.
How WBG Can Help
As shown in the HEV diagram above, power electronics and energy storage take up considerable space on board modern EVs. Further, they contribute significant weight to the vehicle, increasing the amount of energy required to accelerate. The inverter, on-board charger, and additional power electronics and controls for the 2013 Camry, shown at right, weigh over 70 pounds and occupy a combined volume of over 23 liters. In addition to these components, additional cooling systems are needed to prevent overheating of the power converters.
Because of their improved material characteristics, WBG devices can help to reduce the size and weight of the power conversion stages while maintaining or increasing their efficiency. In the case of the on-board charger, WBG devices can enable higher switching frequencies, which will reduce the sizes of passive components. In the case of the motor driver inverter, the motor itself will dictate the switching ripple, and therefore a higher switching frequency will not result in the same benefits. However, WBG may be able to enable new motor designs which result in an overall smaller and more efficient electric drive system.
Further, WBG materials, and SiC in particular, have much higher thermal conductivity and better high temperature performance than silicon. This characteristic can be leveraged to reduce or eliminate dedicated cooling loops for the vehicle power electronics, resulting in cascaded benefits to vehicle size, weight, and cost.
Beyond improving the existing systems, WBG devices are enabling new applications for electric vehicles.
- Wireless power transfer shown in the video below, uses high frequency converters to generate magnetic fields which allow an electric vehicle to be charged without the need for a physical plug. WBG devices enable sufficiently low switching energy loss to achieve efficiencies of wireless charging comparable to that of traditional wired chargers.
- LiDAR (Light Distance and Ranging) uses pulsed later diodes and light sensors to measure distance between the unit and the nearest physical object, allowing local 3D vision in smart vehicles. The resolution of LiDAR systems is dependant upon the duration and integrity of the pulsed current which supplies the laser diode. WBG devices, with their faster switching speeds, enabling better resolution and accuracy
- Radiation Hardened electronics are critical for space applications where systems are exposed to ionizing radiation. WBG semiconductors are inherently less susceptible to radiation, resulting in more reliable and lighter weight (by removing additional shielding) systems for aerospace applications.
Research Projects at UTK
- SiC-Based Reconfigurable DC-DC Converter Design for Electric Vehicles (EV) Charging and Powertrain Application.
- Intelligent Comprehensive Design and Operation Paradigm for WBG-Based Converters
- Intelligent Gate Drive for Maximizing Performance and Enhancing Reliability of Wide Bandgap Semiconductors
- Ultra-light Highly Efficient MW-Class Cryogenically Cooled Inverter for All Future Electric Aircraft Applications
- WBG-based Power Module for EV Traction Drives
- Application of Hybrid Switches (GaN + Si) to the >97%-efficiency 7.2kW Level-2 Charger
- A high-power SiC based bidirectional EV off-board fast charging module
- Coil Design for Wireless EV Charging
- Wireless Power Transfer Loss Simulation and Demonstrator for Electric Vehicle Fast Charging
- Research and Development of An FPGA based Three-phase High-efficiency SiC Inverter for Electric Vehicles
- Benchmark and Design Multi-functional EV Chargers Using WBG Devices For Magna Internationals
- GaN 800V Module with Double Sided Cooling in a 3L Half Bridge Configuration
- A High-efficiency and High-power-density DC/DC Converter Using SiC MOSFETs For Future Autonomous and Connected Vehicles
- Using FPGA to Control Six-phase PMSM and Externally Excited Motors Fed by SiC Inverters
- A High-Efficiency, High-Power-Density Integrated DC/DC with OBC Using SiC and GaN Devices for Electric Vehicles
- Packaging A Top-cooled 650V/300A GaN Power Module with Insulated Thermal Pads and Gate-Drive Circuit
- A High Frequency Wireless Power Transfer System for Electric Vehicle Charging Using Multi-layer Non-uniform Self-resonant Coil at MHz
- Smart, Compact, Efficient 500kW DC Extreme Fast Charger (XFC)
- A Smart and Highly Compact Power Electronics Box to Provide Universal Charging Technologies (OBC, Wireless and DC Fast Charging) along with DCDC
- Integrated Three-level GaN Inverter and PMsynRM Motor for Electric Passenger Vehicles and Medium/heavy duty Trucks (GaNIn_PMsynRM)
- Software Development of Two-level and Three-level Inverter Control for Mercedes Benz R&D North America
- Characterization and Test of Diamond Foundry’s SiC Inverters for Mercedes-Benz
- An EV Auxiliary Power Module with Wide Input and Output Voltage Range Using GaN and Planar Magnetics
- A 48V/12V DC/DC Converter for Electric Vehicles
Commercial Developments
- (03/21) Vitesco Technologies To Supply 800V SiC Inverters For Hyundai Motor Group
- (06/20) Continental to expand use of SiC in power electronics
- (06/20) Aerospace GaN power company re-booted
- (04/20) SiC Used in 900V Motor Drive in New Lucid Motors Production Vehicle
- (12/19) Selecting GaN transistors for avionics power
- (02/18) Advantages of Using Gallium Nitride FETs in Satellite Applications
- (09/14) Hitachi presents a full SiC inverter for EV
- (05/14) Toyota Develops New Silicon Carbide Power Semiconductor with Higher Efficiency